




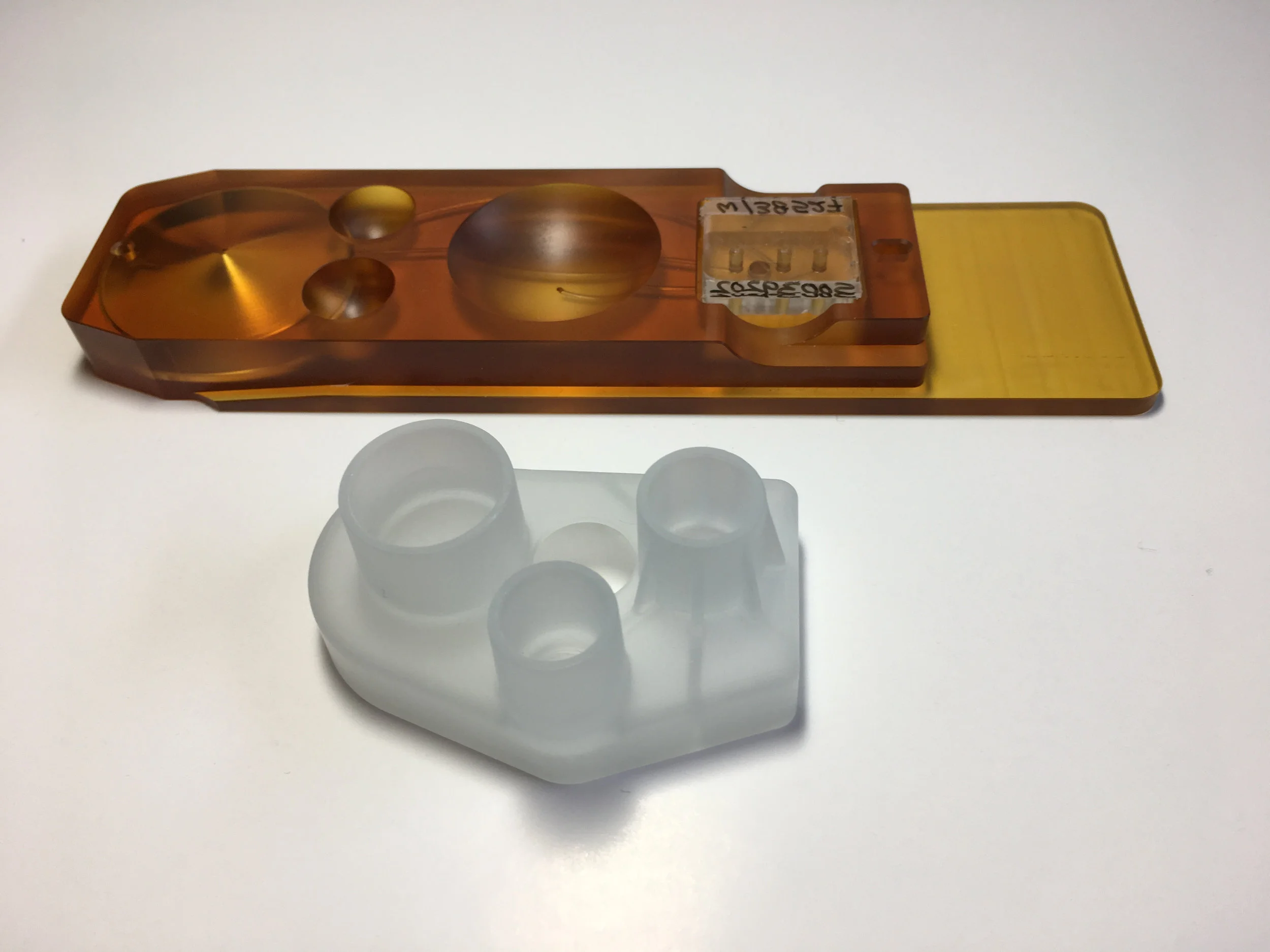








The original concept for the dropmaking vessel. This is a bonded ULTEM assembly, the bonding creates the channels that feed the microfluidic device and also forms the "Inverse funnel" outlet well. This design leverages the buoyancy of the emulsion in the carrier oil in order to extract the emulsion in a controlled manner from a single point (top of the inverse funnel). My prototype for this concept is shown here. This inverse funnel device is the basis around the design for the emulsification and extraction modules shown here.

The bottom of the bonded assembly showing the routing to and from the microfluidic interface.

The microfluidic device (PDMS) is pressed onto the barbed mounting posts shown here. The pattern is keyed to ensure proper installation. There is a through-hole in the ULTEM for imaging the area of interest.

The inverse funnel design was not intended to be a consumable. Coming up with a method that reliably cleans the internal features (especially inverse funnel) proved to be problematic. I designed the injection molded concept with this in mind. It can be cleaned and reused or can be a consumable at higher volumes. The aqueous well is ribbed with the anticipation of sealing the well on the top rim during emulsification.

The microfluidic interface was moved to the bottom. The main advantages are in seal integrity and consistent objective height. Ribs can be seen on the B side of the mold.

Made improvements to handling, added locating features, added further reinforcement based on analysis.