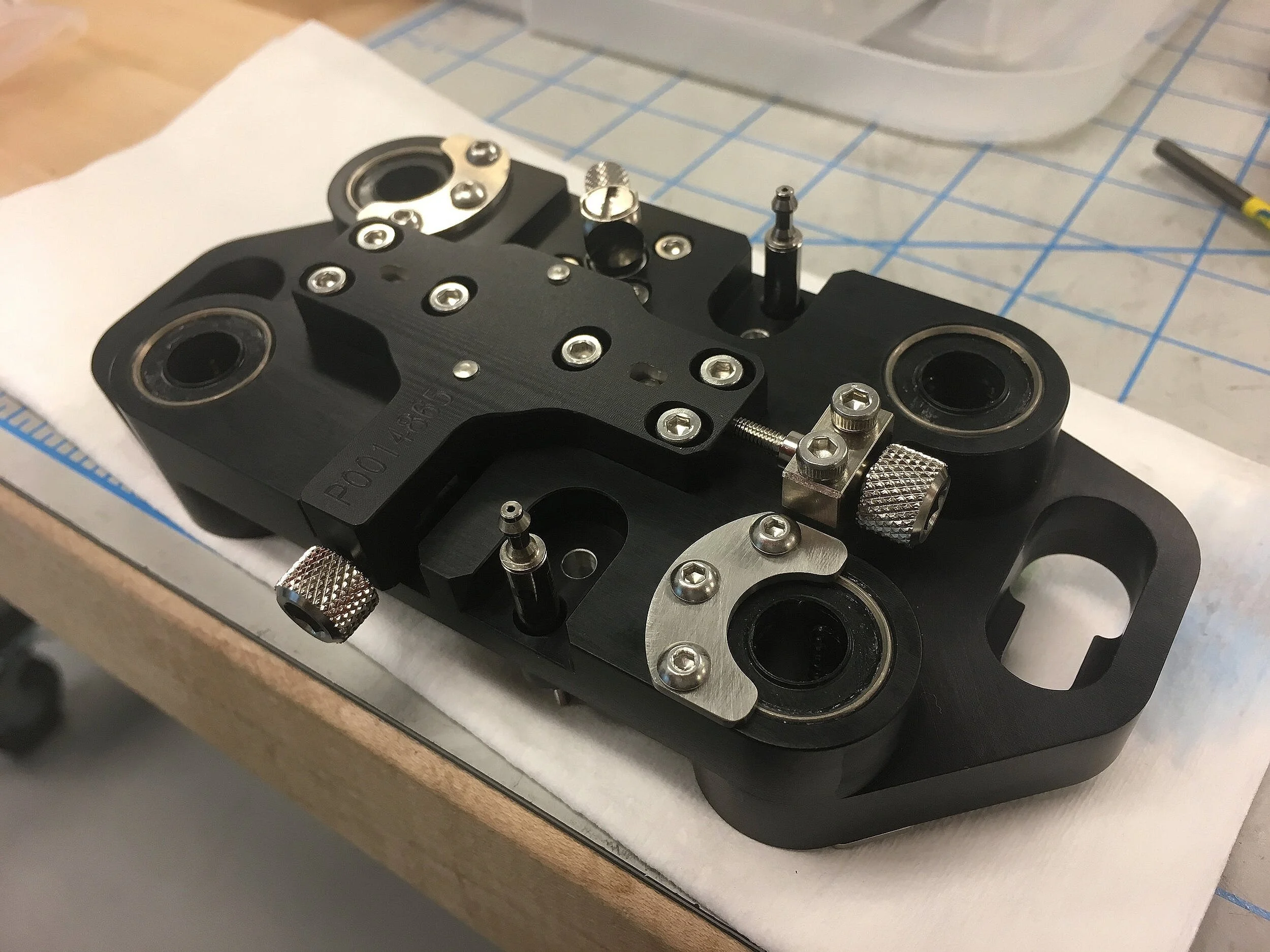

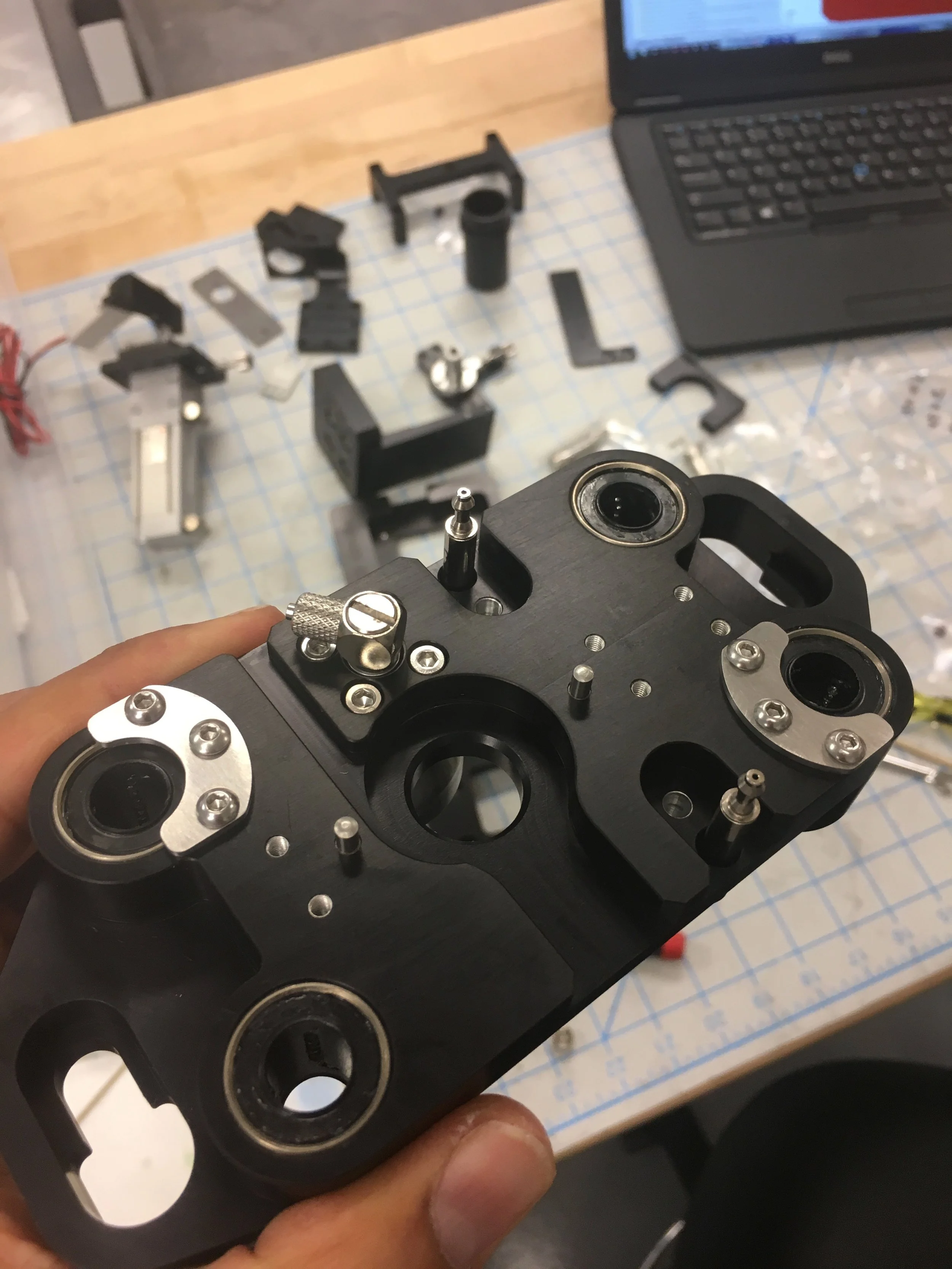



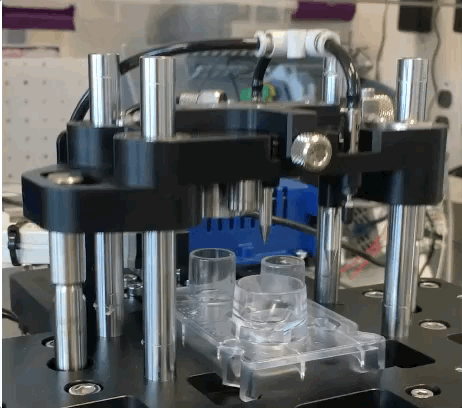
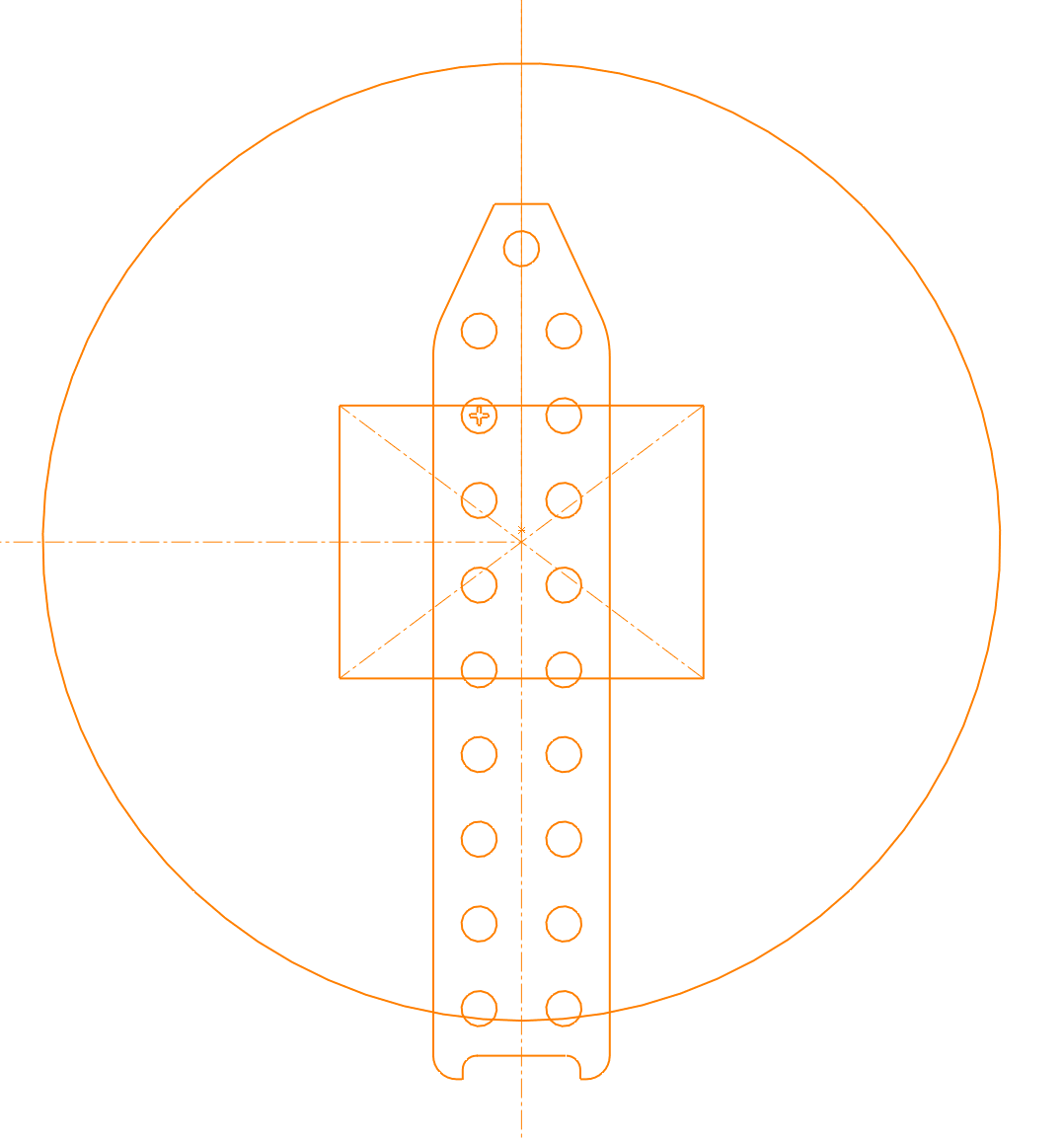

Stepper-driven focusing stage designed around crossed-roller bearing stage. Prototype shown here.
A modular system to automate the production of library emulsions later used in a DNA sequencing platform.
Side view. Each module has the ability to be pulled out of the machine for maintenance service or replacement.
The module was designed to be as compact as possible in front in order to accommodate as many modules side by side as possible in an array.
The pneumatic components are shown here under the electrical enclosure along with the routing.
Quick connect power, ethernet, HDMI, valved quick connect for air and vacuum, leak proof valved quick connects for oil supply and waste.
This is the lab consumable macro/microfluidic device being used in this module. The evolution of this concept is highlighted here.
A precision clamping mechanism that aligns the microfluidic device with the optics. Optics sub-assembly is initially aligned to clamp using precision reticle. System has been toleranced such that the area of interest on any inserted microfluidic device is guaranteed to land within the camera's field of view without re-alignment. This eliminates the need for x/y stages in the assembly.
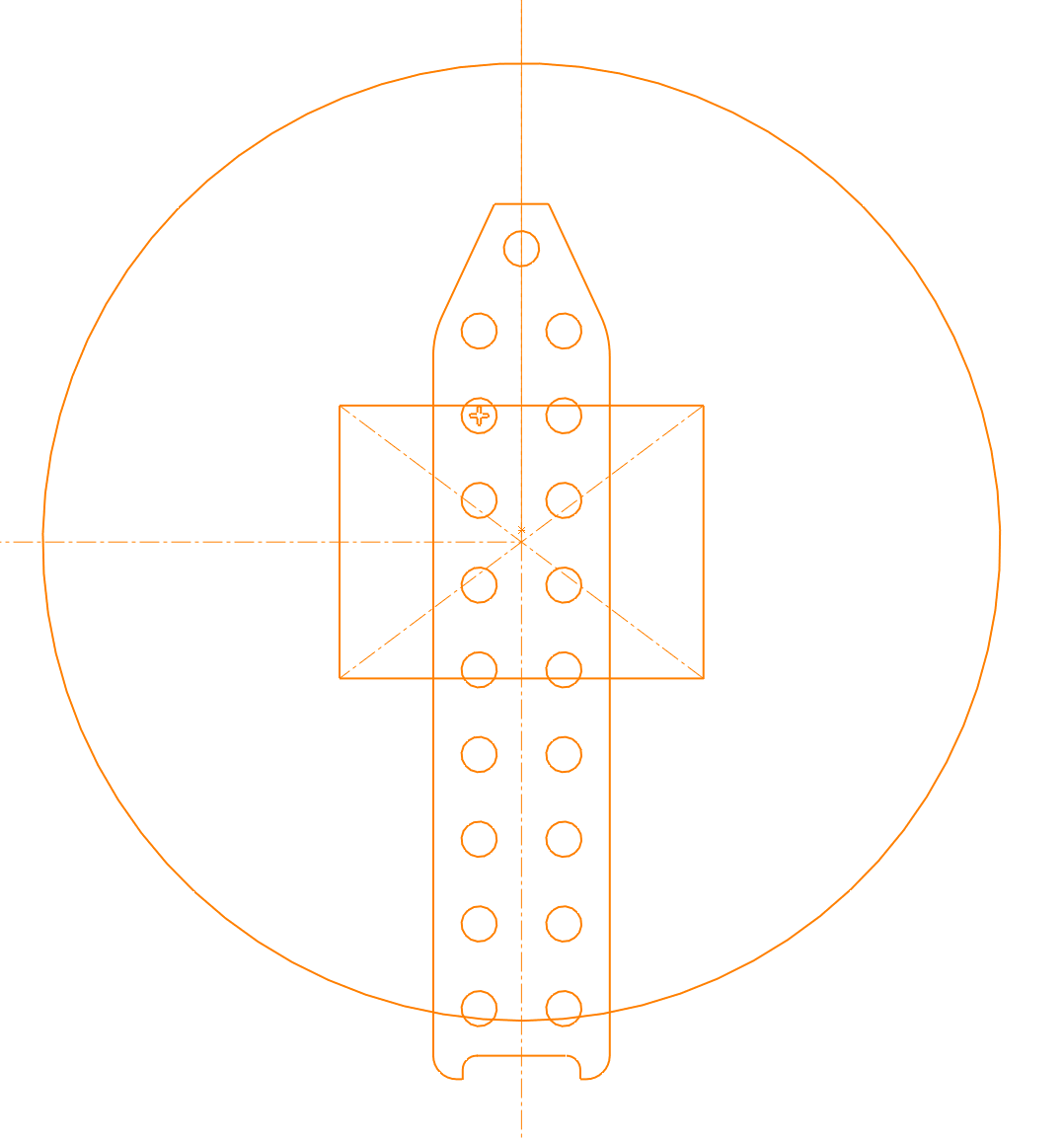
This GIF is the graphical result of my in-depth tolerance analysis for the clamping system. All machined part tolerances, assembly outcome tolerances, injection molding tolerances of the caddy, microfluidic casting fixture mechanical tolerances, possible microfluidic casting temperature variations and resultant PDMS shrinkage calculations were taken into account to ensure that the area of interest ends up within the field of view (stationary rectangle).